Rondloop van verspanend gereedschap
Met rondloop bedoelt men de slingering van een roterend gereedschap ten opzichte van diens rotatiecentrum of hartlijn. Deze slingering is een afwijking of fout in de cirkel die een gereedschap van een bepaalde diameter per omwenteling in het radiale vlak omschrijft. Ter verduidelijking: iedere tand van een Ø16 mm (nominale maat) frees hoort in een cirkel van precies 8 mm radius te draaien, bij iedere omwenteling van de machinespil. In realiteit wijken de verschillende tanden hier echter iets vanaf.
Radiale rondloop of excentriciteit van verspanend gereedschap is gangbaar bij bewerkingen met meerdere snijkanten in een onderbroken snede, zoals freesprocessen. Het kan een gevolg zijn van onnauwkeurigheden in de productie (slijpen) van het gereedschap, afwijkingen in geometrie of concentriciteit, imperfect spangereedschap of statische en dynamische afwijkingen in de freesmachine. [1] Rondloopfouten zijn direct van invloed op de maatvastheid en oppervlaktekwaliteit van het eindproduct, maar vooral ook op de standtijd van het gereedschap.
Rondloop en standtijd
Het effect van rondloop op standtijd is in praktijkonderzoek bij een gevoelige bewerking getest. Hier zijn boren van 3 mm met verschillende rondloopfouten ingezet. Door de rondloop te verbeteren van 1,5 µm naar 0,2 µm bleek dat de levensduur 300% verbetert bij een VHM boor. Snelstaal HSS is door een hogere taaiheid wat vergeeflijker voor rondloopafwijkingen. Maar bij een gelijke verhoging van de rondloopnauwkeurigheid krijgt zelfs een 3xD HSS boor hier een 230% betere levensduur. Bij een 5xD HSS boor met intern koelkanaal was dit een verbetering van 160% in standtijd. Hardmetaal blijkt hier dus het meeste gevoelig voor rondloopafwijkingen. Let wel: VHM had hier een bijna 3x zo hoge snijsnelheid. VHM kan wel degelijk een langere levensduur hebben dan HSS, maar alleen bij hoge rondloopnauwkeurigheid.
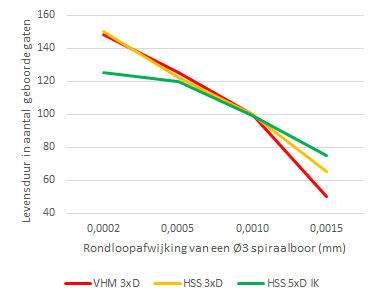
Figuur 1: Standtijd van Ø3 mm boren* in gemaakte gaten
Een verbetering van 1,3 µm in rondloop kan zorgen voor wel 300% levensduur bij uw verspanende gereedschappen !
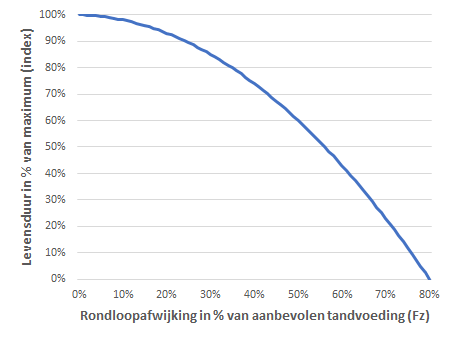
Figuur 2: Deze grafiek toont een veelgebruikte duimregel voor max. standtijd t.o.v. rondloop in % van tandvoeding
* De boren zijn ingezet op C55 (1.1203) materiaal in 3xD=12 mm of 5xD=15 mm (IK) bij snijsnelheid Vc=76 m/min voor VHM of Vc=27 m/min voor HSS en voedingsnelheid F=0,1 mm/omw
Rondloop en snijkracht
Zoals bovenaan uitgelegd, resulteren rondloopfouten in ongelijke effectieve tandradiussen. Doordat het werkstukmateriaal daarmee niet gelijkmatig verwijderd wordt, beïnvloedt dit de snijkrachten die optreden tijdens het verspanen. Daarnaast neemt de materiaalvoeding van een tand toe, en daarmee de slijtage ervan, naarmate zijn effectieve radius groter is dan andere tanden van dezelfde frees. En toenemende gereedschapslijtage heeft weer een verhogend effect op de snijkrachten die ontstaan.
Deze vicieuze cirkel wordt hieronder nader toegelicht. Daar worden twee frezen met ieder acht snijkanten (Z=8) vergeleken: frees T1 heeft een lage rondloopafwijking en frees T7 heeft een relatief hoge rondloopafwijking. De grafieken tonen de verschillen in snijkracht, gedurende drie omwentelingen, in nieuwstaat en na slijtage. [1]
Snijkracht van nieuw gereedschap
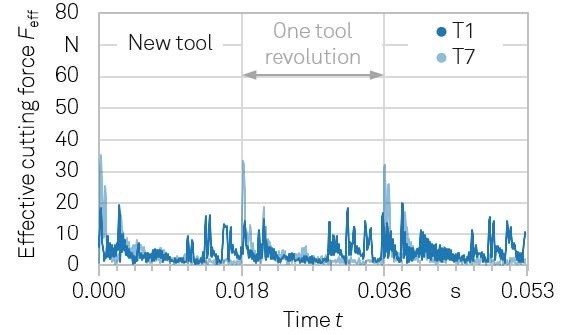
Figuur 3: Snijkracht van de frezen T1 (lage rondloopfout) en T7 (hoge rondloopfout) gedurende drie omwentelingen. Hier zijn deze frezen nog nieuw, dus zonder enige slijtage.
Snijkracht na freespad van 45 meter
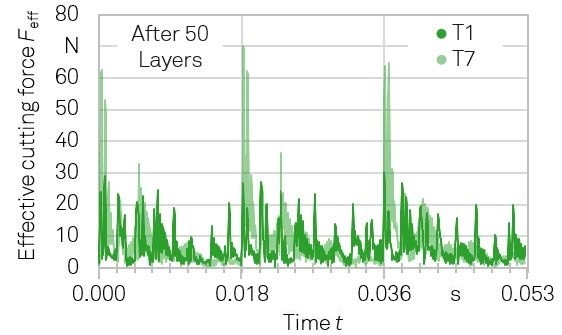
Figuur 4: Snijkracht van de frezen T1 (lage rondloopfout) en T7 (hoge rondloopfout) gedurende drie omwentelingen, nadat ze 50 lagen gefreesd hebben; slijtage is ontstaan.
Snijkracht na freespad van 90 meter
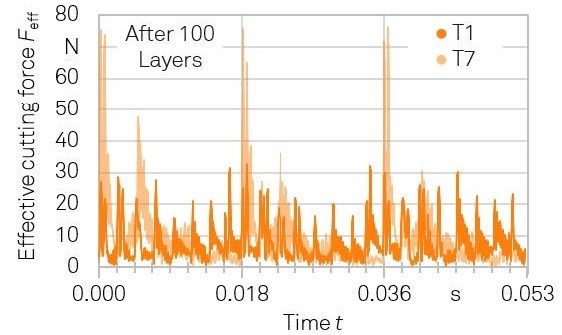
Figuur 5: Snijkracht van de frezen T1 (lage rondloopfout) en T7 (hoge rondloopfout) gedurende drie omwentelingen, nadat ze 100 lagen gefreesd hebben; er is forse slijtage.
Er is te zien in Figuur 3 dat een frees met hoge rondloopafwijking (T7) in nieuwstaat reeds meer belast wordt dan een frees (T1) met een lage rondloopafwijking. De frees T7 ondervindt snijkrachten van meer dan 30 kN en dat is ruim 50% meer dan frees T1 die onder de 20 kN blijft. Maar nog veel belangrijker: bij frees T7 is per omwenteling (tussen de verticale strepen) slechts één piek te zien. Dat wil zeggen: één tand van frees T7 verricht nagenoeg alle verspaning. Deze tand steekt verder uit dan andere tanden (zijn effectieve radius is groter) en krijgt zo ook de materiaalvoeding die eigenlijk voor de andere tanden is bedoeld. Het verschil met frees T1 is groot: bij de kleinere rondloop zijn wel 5 tot 6 pieken te zien, met min of meer vergelijkbare snijkracht; er zijn dus meer tanden, gelijkmatiger in snede.
Er is te zien in Figuur 4 dat een frees met hoge rondloopafwijking (T7) door slijtage sneller een hogere belasting ontwikkelt. De maximale snijbelasting van deze frees is al meer dan verdubbeld (tot 70 kN) ten opzichte van nieuwstaat. Dit terwijl frees T1 met lage rondloop slechts van 20 kN naar 30 kN snijkracht is gegaan. Bij die frees zien we inmiddels ook 8 pieken: na enige slijtage verspanen alle 8 tanden van frees T1 daadwerkelijk. Dit terwijl frees T7 slechts twee duidelijke pieken laat zien: de belasting van deze frees wordt nog steeds niet goed verdeeld over de diverse tanden. De spaanvorming zal onregelmatig en ongelijkmatig verlopen.
Er is te zien in Figuur 5 dat de verschillen in belasting tussen frezen met sterk afwijkende rondloopnauwkeurigheden blijven bestaan, zelfs na langere bewerking. De snijkrachten nemen onder invloed van slijtage weliswaar iets toe, maar verder is deze grafiek nagenoeg hetzelfde als Figuur 2 waar de inzetduur half zo lang is.
Rondloop beïnvloedt snijkracht
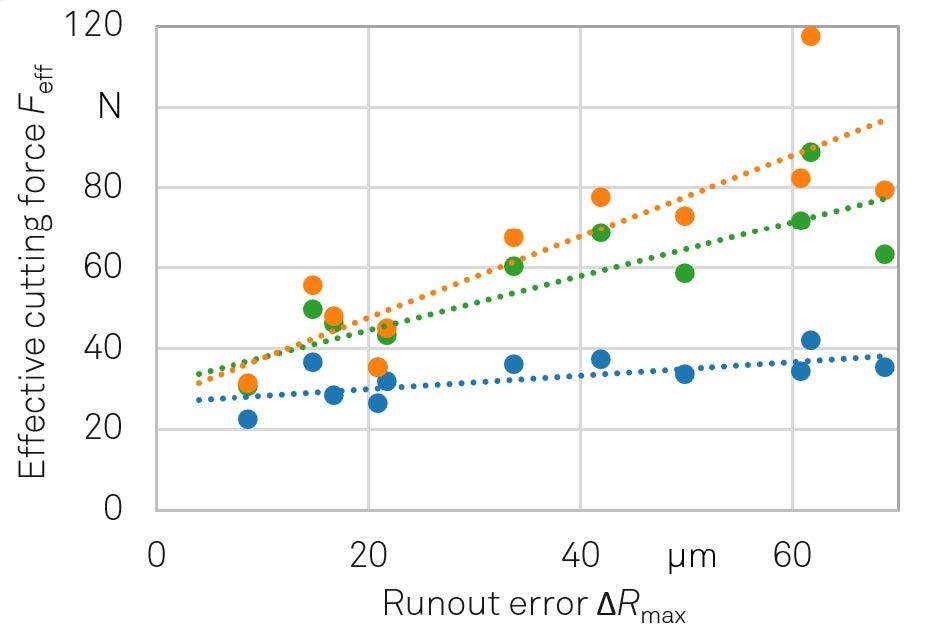
Figuur 6: Effectieve snijkracht van elf geteste frezen, in nieuwstaat (blauw), na 50 (groen) en 100 lagen (oranje) gefreesd, ten opzichte van hun oorspronkelijke rondloop.
Rondloop beïnvloedt slijtagevorming
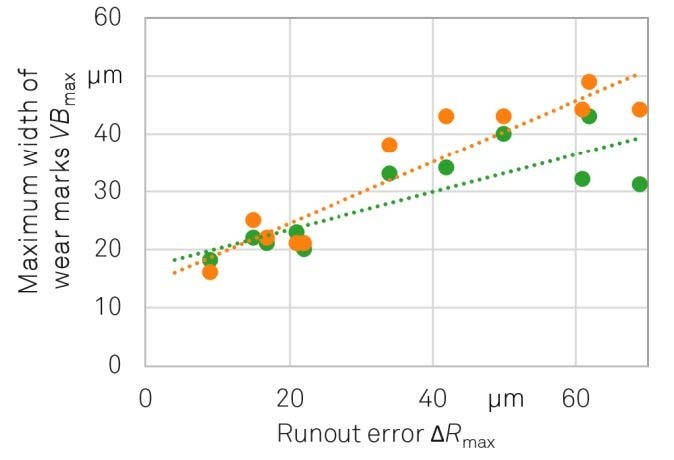
Figuur 7: Maximale breedte van de vrijloopvlakslijtage op iedere geteste frees, na 50 (groen) en 100 (oranje) lagen gefreesd, ten opzichte van hun oorspronkelijke rondloop.

Figuur 8: Het slijtagebeeld van een frees (T7) met hoge rondloopafwijking. Tand 1 heeft de hoogste afwijking (+22,3 µm) en ondervindt de meeste belasting en slijtage.
Hierboven ziet u nogmaals duidelijk dat de snijkracht toeneemt naarmate een frees meer rondloopafwijking heeft (Figuur 6) en dat deze belasting bij inzet toeneemt. En zoals eerder aangegeven leidt deze hogere belasting tot meer slijtage, waardoor rondloop dus direct invloed heeft op de slijtagevorming (Figuur 7) van een frees. Dit komt voornamelijk door een ongelijkmatige belasting. Herinnert u zich de pieken in snijkracht van frees T7 uit Figuur 3-5 nog? Het resultaat is in Figuur 8 te zien. De tand die deze snijkrachtpieken veroorzaakte (tand 1) is vergaand versleten, terwijl de overige tanden er nog relatief goed uitzien. Zou de snijkracht beter over de diverse tanden verdeeld zijn geweest, dan werd de last beter verspreid en zou geen enkele tand zover als tand 1 versleten zijn. En zo gaat de hele frees langer mee.
Bepaalde bewerkingen zijn extra gevoelig voor rondloop
Vooral bij freesbewerkingen met kleine spaandikte en -snede, zowel radiale (Ae) snedebreedte als axiale (Ap) diepte, kunnen rondloopfouten problematisch zijn. Dit zien we bijvoorbeeld bij het microfrezen of het nafrezen van grote complexe vormen zoals titanium turbinebladen of schoepenwielen. In dergelijke gevallen heeft het gereedschap ook vaak een hoge lengte-diameter verhouding (5xD of meer) waardoor de rondloopafwijkingen doorgaans groter zijn. Excentriciteit neemt namelijk toe naarmate iets verder uitsteekt. Denk aan de toren van Pisa: de eerste paar meter van de grond lijkt alles nog niet zo scheef, maar bovenaan wel! Bij hoge excentriciteit bestaat het risico dat de rondloopafwijking groter wordt dan de ingestelde voeding (Fz) per tand. Zodra dit zo is, zal minstens één tand geen materiaal verwijderen, terwijl tenminste één andere tand een hogere belasting heeft. En juist dat leidt tot meer slijtage, dus een kortere levensduur van de frees!
Grotere diameters zijn beter bestand tegen rondloopfouten
Natuurlijk speelt de grootte van het gereedschap een rol in het effect van rondloopfouten op standtijd. De hogere massa van een groter gereedschap, onder invloed van de lengte-diameter verhouding, heeft invloed op de krachten die bij de verspaning optreden. Daarom kan het zo zijn dat twee verspanende gereedschappen met precies dezelfde rondloopnauwkeurigheid maar andere diameters compleet andere resultaten opleveren. Over het algemeen kunnen we stellen: hoe groter het gereedschap, hoe meer rondloopafwijking deze kan verdragen. Dit heeft vooral te maken met de voeding (Fz) per tand, wat bij groter gereedschap doorgaans hoger kan en mag zijn. Deze tandvoeding wordt namelijk bepaald met een zekere maximale belasting (snijkracht en spaandikte) voor ogen. Indien een rondloopfout ervoor zorgt dat bepaalde tanden meer belast worden dan dit maximum, dan neemt hun levensduur af.
Hoe verbeter ik de rondloopnauwkeurigheid?
Om de snijkanten in snede met een zo hoog mogelijke rondloopnauwkeurigheid te laten verspanen, dient echt alles tot aan het einde van de uitsteeklengte te kloppen. Hiermee wordt in feite alles bedoeld wat tussen de snijkant en de machine zit: de machinespindel moet met zo min mogelijk afwijking in rondloop roteren, de machine-opname moet onbeschadigd en vrij van vervuiling zijn, de gereedschapopname ook, en men dient te kiezen voor een spanwijze met weinig inherente rondloopfouten.
Zorg dat uw machinespil in goede conditie is
Allereerst dient u zich ervan te verzekeren dat de opname in de machine schoon is. Vervuilingen zoals stof, uitgeharde olieresten en kleine spaantjes kunnen er allemaal voor zorgen dat een gereedschapopname niet perfect recht in de machine komt te zitten. Het voorkomen van dergelijke scheefstand kan vaak de allereerste winst zijn. Controleer en reinig dus alle oppervlakken van de machineopname, daar waar deze in contact komen met uw gereedschapopnames, grondig en met enige regelmaat.
Controleer de spindel met een meetdoorn
Bovendien kan de machinespil, als gevolg van stelselmatige en langdurige belasting, zelf ook rondloopafwijkingen ontwikkelen. En zelfs de beste gereedschapopname kan geen optimale prestaties leveren, als deze in een onnauwkeurige of versleten spindel wordt gebruikt. Door de machinespindel regelmatig op rondloopafwijkingen te controleren, kunt u potentiële problemen in een vroeg stadium identificeren. Dit kunt u doen door gebruik te maken van een speciale meetdoorn: een uiterst precies geslepen staaf met lange uitsteeklengte en een opname geschikt voor uw machine. Na het monteren van de meetdoorn in uw (gereinigde) machineopname, kunt u met een meetklok nagaan hoe nauwkeurig de rondloop van uw spindel is. En kijkt of deze metingen binnen de voorschriften of specificaties van de machinefabrikant vallen. Machinefabrieken die dit consequent doen, zijn altijd op de hoogte van de kwaliteit in hun spindel en kunnen zo voorbarig onderhoud en machinestilstand voorkomen.
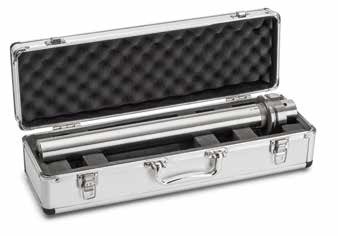
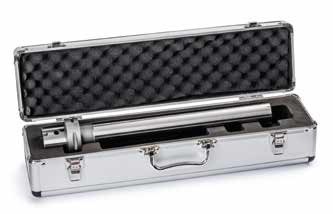

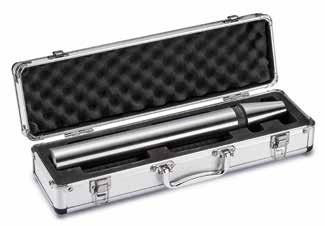
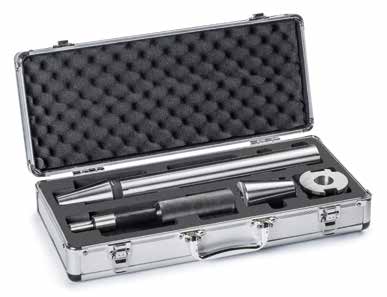
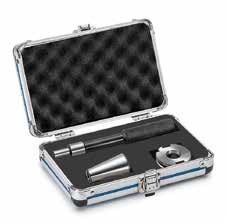
Gebruiksaanwijzing: De taster van uw meetklok laat u op een bepaalde uitsteeklengte de meetdoorn raken, zodat de taster iets onder veerdruk staat. Bijvoorbeeld tot de klok 0,2 mm aangeeft. Vervolgens draait u de spil langzaam met de hand rond, waarbij u kijkt hoever de meetklok uitslaat. U noteert de minimaal en maximaal aangegeven waarde. Het verschil tussen deze twee meetwaarden is de rondloopafwijking, op deze uitsteeklengte van de meetdoorn. Het is aanbevolen om de meting op meerdere uitsteeklengtes te herhalen, voor een vollediger beeld. Bijvoorbeeld 1x aan het begin, 1x circa halverwege en 1x net voor het uiteinde van de meetdoorn.
Vervang eventuele aantrekbouten
Gereedschapopnames met een lange conus, zoals SK en BT, worden middels aantrekbouten in de machineopname vastgetrokken. Deze aantrekbouten of "pullstuds" worden in het uiteinde van de conus op de gereedschapopname geschroefd en zijn vervangbaar. Het zijn relatief eenvoudige en voordelige onderdelen, die men helaas vaak vergeet te controleren. Voor een optimale rondloopnauwkeurigheid is het echter belangrijk dat ook de aantrekbouten in goede staat zijn. Een aantrekbout die niet (meer) correspondeert met de hartlijn van de conus of machinespil, kan zijdelingse krachten op het geheel uitoefenen. Bij verspaning kan dit tot rondloopafwijkingen leiden. Dit dient men te voorkomen, door defecte aantrekbouten zo snel mogelijk te vervangen. Een goede aantrekbout is gemaakt van sterk metaal dat enigszins gehard en zeer nauwkeurig op norm is geslepen. Op die manier kunnen ze plastische vervorming langer weerstaan en komen ze nauwkeurig in positie op de machine.
Kies opnames met hogere rondloopnauwkeurigheid
Bij gereedschapopnames is een hoge rondloopnauwkeurigheid van extra belang, omdat de rondloopfout groter wordt naarmate het gereedschap verder van de houder uitsteekt. Zo kan een opname met een rondloopnauwkeurigheid van 0,01 mm (bijvoorbeeld een spantangopname) al gauw resulteren in een rondloopfout van 0,02 tot 0,03 mm aan de snijkanten van het ingespannen gereedschap. De rondloopafwijking van de opname versterkt zich als het ware, door de lengte van het gereedschap. Er zijn verschillende manieren om gereedschap te spannen, waarbij de gekozen spanwijze en opname bijdraagt aan de totale rondloopnauwkeurigheid. Een overzicht:
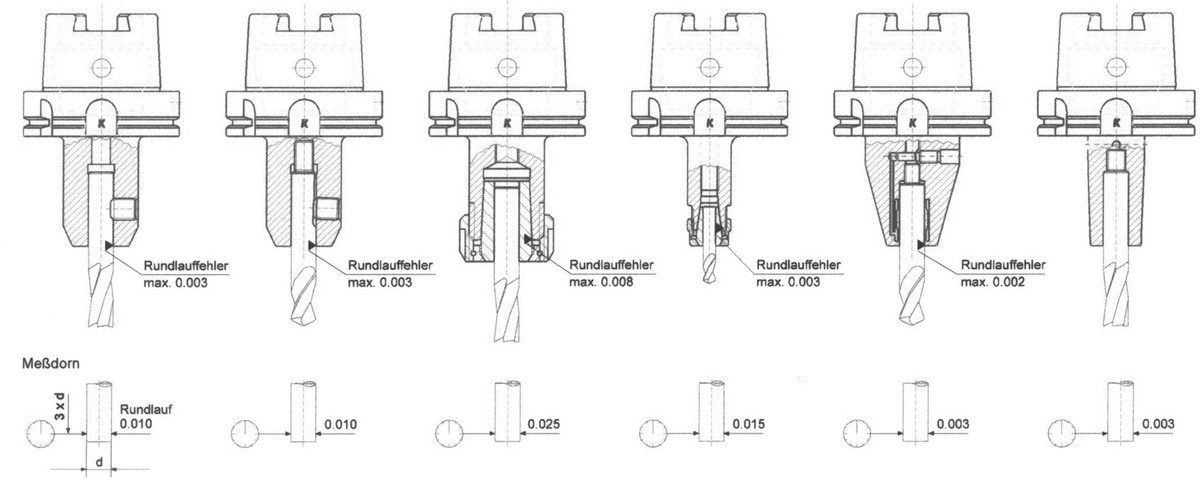
Figuur 9: Gangbare rondloopnauwkeurigheden voor verschillende soorten gereedschapopnames. Door de uitsteeklengte van het gereedschap nemen deze rondloopafwijkingen toe.
Verspanend gereedschap heeft ook rondloop
Het verspanend gereedschap zelf heeft ook een rondloopnauwkeurigheid. Zo kan een frees bijvoorbeeld tanden hebben die meer uitsteken dan andere. Figuur 10 laat dit zien voor twee verschillende frezen van Ø16 mm. De nominale radius van deze diameter is 8 mm (de helft) en idealiter steken alle tanden precies zover uit ten opzichte van het middelpunt. Deze ideale situatie wordt door de stippellijn aangegeven. Daarnaast toont die grafiek twee frezen (T1 en T7) met verschillende rondloopnauwkeurigheden. U ziet duidelijk dat frees T1 (donkerblauw) nauwelijks afwijkt van nominaal.
Daarentegen heeft de frees T7 (lichtblauw) slechts twee tanden dichtbij nominaal liggen. Verder heeft deze frees drie tanden die ver onder- en drie tanden die ver buiten de nominale radius uitsteken. Deze frees T7 wordt dus enorm ongelijkmatig belast bij het verspanen! Alle snijkracht komt aanvankelijk (voordat slijtage optreedt) op slechts enkele tanden te staan, waarbij tand 1 zelfs verreweg het meeste wordt belast. Het effect daarvan kunt u duidelijk zien in Afbeelding 1 bovenaan: die ene tand is na inzet volledig versleten, terwijl de rest nauwelijks enige slijtage laat zien.
Dit is een van de renenen waarom frezen ook een tolerantie op hun eigen afmetingen hebben. Er bestaan verschillende classificaties, waarbinnen de specifieke toleranties aangeven hoeveel afwijking van de nominale maat nog acceptabel is. Nauwe maattoleranties zorgen voor een gelijkmatiger freesproces (standtijd) en meer maatvastheid in het eindproduct.
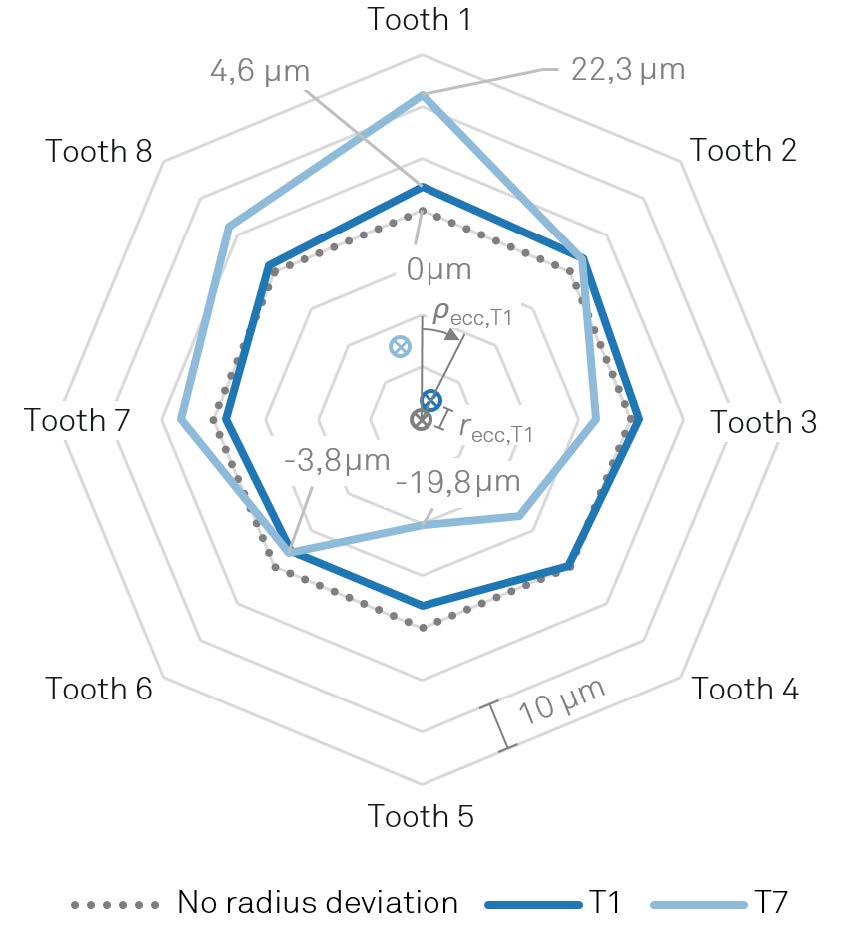
Figuur 10: Tandspecifieke rondloopfout [1]
Hoe nauwkeurig is de diameter?
Voor de maatvastheid van het uiteindelijke product dat men verspaant, wordt vaak gelet op de maattolerantie van een gereedschap. Zo wordt voor nauwkeurige kleine spiebanen bijvoorbeeld vaak een js9 tolerantie gehanteerd: een vrij nauwe tolerantie die symmetrisch (zie Figuur 11) om de nominale afmeting is verdeeld.

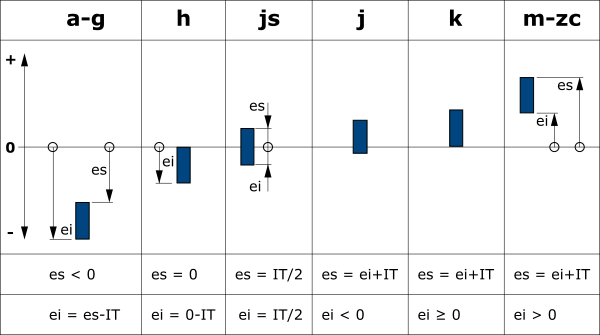
Figuur 11: Tolerantieklassen voor de buitendiameter van cilindrische vormen (ISO 286-2)
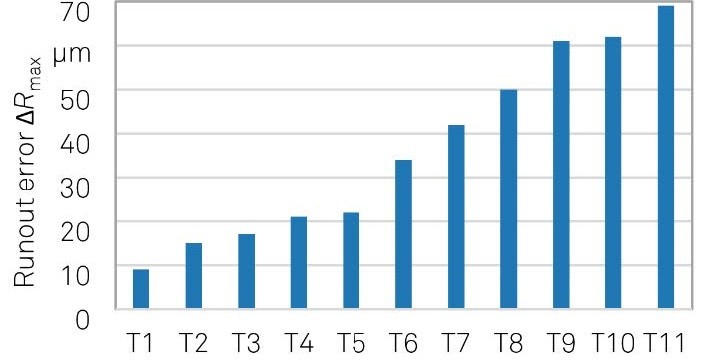
Figuur 12: Voor elf verschillende frezen (T1-T11) van Ø16 mm is het maximale verschil in rondloop tussen hun (Z=8) afzonderlijke tanden bekeken. [1] Zou je dit zien als afwijking t.o.v. de nominale diameter, dan zou dit type frees net binnen een IT10 tolerantie vallen.
Voor een gelijkmatige belasting van het gereedschap (dus levensduur) is echter de IT tolerantie het belangrijkste. Dit is het verschil tussen de grootste afmeting (es) en de kleinste afmeting (ei) die nog binnen de betreffende tolerantie vallen. Dat verschil wordt indirect aangegeven door het cijfer van de maattolerantie: over het algemeen geldt dat een lager getal ook een nauwere tolerantie betekent. Waarom is dit belangrijk: u kunt zich voorstellen dat naarmate een frees in diameter minder mag variëren, dat het verschil in rondloop tussen de tanden onderling ook kleiner is. En eerder heeft u al gelezen dat dit de standtijd enorm kan verhogen!
Toleranties volgens ISO 286-2
In onderstaande tabellen kunt u zien hoe verschillende maattoleranties zich verhouden tot de IT classificaties. Stel bijvoorbeeld dat een Ø16 mm frees maximaal 70 µm in deze nominale diameter varieert. Deze frees valt in de rij van Ø10-Ø18 mm waarbij 70 µm nog net aan de IT10 tolerantie voldoet. Indien ook nog blijkt dat deze frees nooit groter is dan exact Ø16 mm (de afwijkingen zijn 0 of negatief) dan is dit waarschijnlijk een h-tolerantie, zoals in Figuur 11 te zien is. In dat geval valt de 70 µm van IT10 in een bereik van +0 tot -70 µm ten opzichte van de nominale maat. Wellicht niet verrassend: dit blijkt een h10 tolerantie te zijn!
Ø (mm) | IT01 | IT0 | IT1 | IT2 | IT3 | IT4 | IT5 | IT6 | IT7 | IT8 | IT9 | IT10 | IT11 | IT12 | IT13 | IT14 | IT15 | IT16 | IT17 | IT18 |
0 t/m 3 | 0,3 | 0,5 | 0,8 | 1,2 | 2 | 3 | 4 | 6 | 10 | 14 | 25 | 40 | 60 | 100 | 140 | 250 | 400 | 600 | 1000 | 1400 |
3 t/m 6 | 0,4 | 0,6 | 1 | 1,5 | 2,5 | 4 | 5 | 8 | 12 | 18 | 30 | 48 | 75 | 120 | 180 | 300 | 480 | 750 | 1200 | 1800 |
6 t/m 10 | 0,4 | 0,6 | 1 | 1,5 | 2,5 | 4 | 6 | 9 | 15 | 22 | 36 | 58 | 90 | 150 | 220 | 360 | 580 | 900 | 1500 | 2200 |
10 t/m 18 | 0,5 | 0,8 | 1,2 | 2 | 3 | 5 | 8 | 11 | 18 | 27 | 43 | 70 | 110 | 180 | 270 | 430 | 700 | 1100 | 1800 | 2700 |
18 t/m 30 | 0,6 | 1 | 1,5 | 2,5 | 4 | 6 | 9 | 13 | 21 | 33 | 52 | 84 | 130 | 210 | 330 | 520 | 840 | 1300 | 2100 | 3300 |
Tabel 1: Maximaal volgens ISO 286-2 toegestaan verschil in microns (µm) tussen de grootste (es) en kleinste afmeting (ei) van een nominale diameter (Ø) op een cilinder.
Ø (mm) | d11 | e8 | h7 | h8 | h9 | h10 | h11 | h12 | js12 | js14 | js16 | k10 | k12 |
0 t/m 3 | -20/-80 | -14/-28 | +0/-10 | +0/-14 | +0/-25 | +0/-40 | +0/-60 | +0/-100 | +50/-50 | +125/-125 | +300/-300 | +40/-0 | +100/-0 |
3 t/m 6 | -30/-105 | -20/-38 | +0/-12 | +0/-18 | +0/-30 | +0/-48 | +0/-75 | +0/-120 | +60/-60 | +150/-150 | +375/-375 | +48/-0 | +120/-0 |
6 t/m 10 | -40/-130 | -25/-47 | +0/-15 | +0/-22 | +0/-36 | +0/-58 | +0/-90 | +0/-150 | +75/-75 | +180/-180 | +450/-450 | +58/-0 | +150/-0 |
10 t/m 18 | -50/-160 | -32/-59 | +0/-18 | +0/-27 | +0/-43 | +0/-70 | +0/-110 | +0/-180 | +90/-90 | +215/-215 | +550/-450 | +70/-0 | +180/-0 |
18 t/m 30 | -65/-195 | -40/-73 | +0/-21 | +0/-33 | +0/-52 | +0/-84 | +0/-130 | +0/-210 | +105/-105 | +260/-260 | +650/-650 | +84/-0 | +210/-0 |
Tabel 2: Maattoleranties volgens ISO 286-2 ten opzichte van nominale diameter (Ø) met toegestane afwijkingen (es/ei) in microns (µm) uitgedrukt. Ter informatie: 1 µm = 0,001 mm.
Bronnen
[1] Baumann, Siebrecht, Wiederkehr & Biermann (2019) The effect of runout errors on process forces and tool wear. Procedia CIRP 79: 39–44